When a problem reoccurs, it’s rarely due to bad luck—more often, it's due to not addressing the root cause. Root Cause Analysis (RCA) is a systematic approach to identifying the underlying cause of a problem so you can fix it once and for all. In manufacturing and operations, mastering RCA is critical to improving quality, safety, and productivity. Yet many teams struggle to go beyond surface-level fixes.
In this blog, we’ll break down the steps, tools, and mindset needed to perform effective root cause analysis—so you can stop firefighting and start solving.
Why Root Cause Analysis Matters?
Without RCA, teams risk implementing temporary fixes that never prevent the issue from happening again. This reactive mode can lead to increased downtime, scrap, customer complaints, and even safety incidents. Worse, it creates a culture where problems are tolerated rather than solved.
Effective RCA flips the script. It digs below symptoms to find what actually caused the failure. Was it a machine issue? A process deviation? A training gap? Once uncovered, teams can implement countermeasures that eliminate recurrence of error.
Beyond immediate problem-solving, RCA also enables:

In Lean and Six Sigma practices, RCA is foundational. It's what turns tools like A3 reports, FMEA, or CAPA plans into high-impact initiatives. Simply put, organizations that excel at RCA solve problems faster—and more permanently—than those that don’t.
There are a lot of professionals that have misconceptions about RCA and 5 Whys problem solving approach. If you want to learn a detailed distinction between RCA vs 5 Whys Problem Solving, refer to our blog that has covered key differences and use cases for both structured problem solving methods.
The Five-Step RCA Process
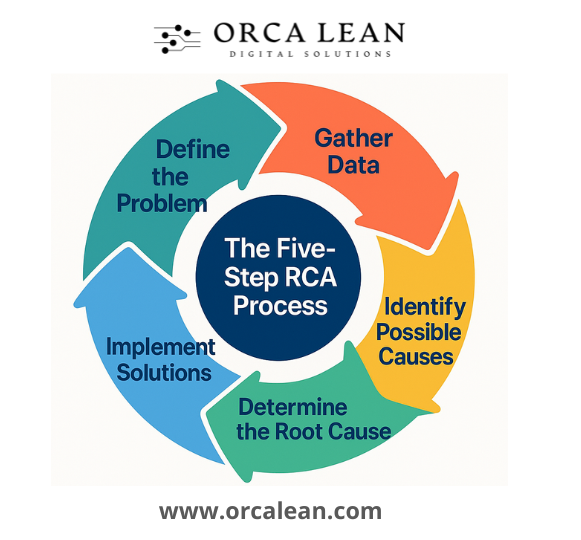
1. Define the Problem Clearly
A precise problem statement ensures that everyone involved in the analysis has the same understanding of what went wrong. If a problem is vaguely described, it can lead to confusion, scope creep, and misdirected solutions.
Key Actions
- Pinpoint the specifics: Quantify the problem in terms of measurable impact—e.g., how much downtime, how many defects, or how many customer complaints.
- Set the context: Include relevant details such as when (date, shift), where (which line, which station), and who (which team or process step) is impacted.
- Align stakeholders: Share the problem statement with all relevant departments (e.g., Operations, Quality, Maintenance) to confirm agreement on the issue.
- Avoid assumptions: Keep the statement factual, focusing on observable reality rather than suspected causes.
Example
- Vague statement: “We’re getting too many defects.”
- Clear statement: “Between March 1st and March 15th, the defect rate on Production Line 3 increased from 2% to 8%, resulting in an average of 40 defective units per day.”
2. Gather Data and Evidence
RCA must be grounded in facts. Data collection prevents “guessing” and helps you zero in on the real problem. Without solid evidence, teams risk wasting time on irrelevant or inaccurate theories. Utilizing Manufacturing Software solutions can help you collect data and track real-time updates.
Want to explore the role of advanced analytics for effective root cause analysis, read our blog that covers 5 reasons why analytics should be used for data tracking and effective root cause analysis.
Key Actions
- Collect quantitative data: Pull production logs, inspection reports, machine readings, and other objective metrics.
- Gather qualitative insights: Conduct interviews or informal conversations with frontline staff, supervisors, and any team members who witnessed the problem.
- Document environmental/contextual factors: Note any external variables—like weather, material changes, new operators, or recent maintenance—that could influence performance.
- Organize findings: Create a central repository (digital or physical) for all data and evidence. Visual aids such as charts or annotated photos can help.
Example
- Production Data: Time-stamped output showing a spike in defects after a new batch of raw materials arrived.
- Operator Feedback: Multiple operators mention that a slight vibration started occurring on the conveyor belt two days before the defects increased.
3. Identify All Possible Causes
It’s easy to latch onto the first “plausible” cause. However, failing to explore all potential factors leads to superficial fixes that don’t solve the real issue. By mapping out all possibilities, you create a complete picture of what might be contributing to the problem. It is the responsibility of quality managers to create root cause analysis a habit at every stage of production.
Explore how quality managers can make ROOT CAUSE ANALYSIS a routine in every stage of production?
Key Actions
- Brainstorm broadly: Invite cross-functional stakeholders (e.g., production, quality, maintenance, engineering) to provide input. Diverse perspectives prevent oversight.
- Use structured tools:
- 5 Whys: Keep asking “Why?” until you uncover a root or systemic cause. Stop only when the answer points to a fundamental process or condition.
- Fishbone (Ishikawa) Diagram: Categorize potential causes under headings like Methods, Materials, Machines, Manpower, Measurement, and Environment.
- Pareto Analysis: If you have historical data for multiple recurring issues, rank them by frequency or severity to see which cause is most critical.
- Look for multiple contributing factors: Often, more than one cause intertwines—like a combination of outdated procedures and untrained personnel.
Example
Potential Causes:
- Machine misalignment (mechanical problem).
- Inconsistent raw materials from a new supplier.
- Operator error due to inadequate training or unclear work instructions.
- Process changes in upstream operation, causing fluctuations downstream.
4. Verify the Root Cause
Not every “why” is the true root cause. If you pick the wrong root cause, your corrective action won’t eliminate the problem. Verification ensures you don’t go down the wrong path.

Key Actions
- Test your hypothesis: If you suspect the issue is due to a misaligned machine, realign it temporarily or switch to a machine known to be aligned. If the problem disappears, you have strong evidence of that root cause.
- Ask critical questions:
- Does addressing this cause explain the entire problem (all symptoms)?
- Is the cause supported by both quantitative data and qualitative feedback?
- Could there be an even deeper cause that led to this issue?
- Use controlled experiments: If possible, run pilot tests with controlled variables to isolate the suspected cause.
- Involve cross-functional validation: Check with different teams or experts for consensus. Sometimes, an alternative viewpoint uncovers missed details.
Example
- Verification in Action: After suspecting that misalignment in the conveyor was the culprit, maintenance staff aligned the belt. The defect rate dropped to previous levels within 24 hours. This strongly indicates alignment was a key root cause.
5. Implement Corrective Actions and Monitor Results
Even with a correctly identified root cause, the full benefits won’t be realized without well-executed corrective actions. Monitoring ensures the fix is effective and remains in place over time.
Key Actions
- Develop a clear action plan: Identify what needs to change (e.g., recheck machine alignment after every maintenance shutdown), who is responsible, and by when the actions should be completed.
- Communicate and train: Inform all affected team members about the changes. Provide training if new procedures or standards are introduced.
- Document changes: Update Standard Operating Procedures (SOPs), work instructions, maintenance schedules, or supplier agreements to reflect the new requirements.
- Track effectiveness: Monitor relevant Key Performance Indicators (KPIs) and gather feedback from operators to see if the issue resurfaces or if there are unintended consequences.
- Establish periodic reviews: Even after success, schedule regular follow-ups to ensure the fix remains effective. Consider audits or spot checks if the risk or cost of recurrence is high.
Example
Corrective Action Rollout:
- The maintenance team introduces a weekly conveyor alignment check.
- Operators receive quick training on identifying early signs of misalignment.
- The quality team collects data for the next four weeks to confirm sustained improvement.
Conclusion
Solving recurring problems starts with finding the real root cause—and Solvonext makes that easier than ever. With built-in RCA tools like 5 Whys, Ishikawa diagrams, and collaborative investigation workflows, your team can move from guesswork to evidence-based problem-solving. No more scattered notes, missed follow-ups, or siloed fixes.
Solvonext keeps your entire RCA process structured, visible, and actionable—so issues get resolved and stay resolved. Ready to stop firefighting and start improving for good? Try Solvonext and see how fast, effective, and scalable your root cause analysis can be. Book a demo today and empower your team to solve smarter.